Thanks a lot for your efforts - we just checked the chamber temperature with a third meter - well, we don´t reach this chamber temperature. After half an hour it stopped at 46.5 degrees (bedtemperature is set to 95). One thing we already determined - the real bed temperature is a bit lower than shown up in Bambu studio, approxiamtly 92 degrees.
We are now running a test with an insulation plate on the top of the machine … actually we are coming up near 50 degree. It´s not looking nice … but there is inside not enough space for insulation.
Hope that helps
My plate temperature is also less than it is set to 90 degrees not 100. I asked Bambu about this and they said a difference of 5-10 degrees is normal. It may be normal but it is not helpful when you want to print at a real 100 not 90 and the P1S only allows a max setting of 100.
I wanted to know more now. Another test print, but I hadn’t calibrated the filament for the Cr-20 and just started printing, so at some point the nozzle was blocked and I had to stop printing. But it is enough to compare the contact surfaces with each other, there is enough material available.
Left in the picture: Cr-20 Pro, ABL, glass plate, 60°C to 68°C bed
On the right in the picture: BBL X1C, Cool Plate, ABL, 30°C to 35°C bed
Both parts were always printed together on one printing plate.
The glass plate isn’t perfectly straight either, but it’s about half as curved as the other one.
i tried printing your file on my p1p and it also warps. you said it prints perfectly flat on your x1 ?
i get similar results with my p1p.
because i needed a printer that could print taller prints, i ordered a FLsun v400.
i tried PETG and it seems a lot less prone to warping on this machine…
It is really beyond me what is the reason that my v400 does this with so much less warping. im really starting to believe printspeed is also a factor in the whole warping process
Yup. I printed using California Filament translucent PETG. The profile I use has 255C / 70C temps and 40%@30s / 100%@3s fan speed (I assume I used the generic PETG profile and perhaps tweaked the nozzle temp a bit).
How did your result look like?
You won’t notice anything crucial here, if anything. If you place something on a surface and photograph it from an angle such as 45°, you will hardly see anything. But a trained eye can still see something. Because conclusions can be drawn from the shadow cast, for which a light gap test is worthwhile. If you do this afterwards, you can see that it is not 100% straight.
This will also be the reason why opinions differ so much. What is good enough for one person and does not cause any problems for the intended design is useless for another.
See the example below, it is perfectly straight. Or not? They are the same objects as shown by me above in this thread. So they are not straight.
Hi, thank you for your reply - well point now : I surrender
Makes no sense to try it further at the moment. Spent too much time and material on this target.
In the last step we wrapped the X with several layers of “plopp” foil and we reached afetr some while a temperarture in the build room of about 50 degrees. Well the warping is better, but it is still there - I think with more efforts in insulation (with a buildroom temperature at 60 or 70degrees, it would work.
As we don´t see this problem with Petg I´ll switch to this material, even if the structure is not so fine
For anybody else who read this, I used Original Bambu ASA and tried to print out a retangular housing front ca. 200X50X40mm- I had warping with 1.5mm on the longer side and tried to fix this.
Best regards to you - and I can confirm with non retangular objects you don´t encounter this problem - and the temperature in the heat chamber should be higher than posible with the X-1 carbon.
Christian
I don’t understand your suggestion, which simply means that you want to circumvent a problem instead of solving it. You want to get around it by trying to use tricks that can possibly improve the outcome of the problem somewhat, that is, that you thwart the consequences of the problem.
Why do you want to change a design that, on the one hand, is no longer the same design and the printed object no longer has the look that you need or were aiming for and, on the other hand, is not the cause of the problem? And how would you like to influence the design of a printed object that is not your design? So when you print someone else’s designs? Even Bambulab does not provide any special designs that can be printed without any problems on their printers.
I would like to remind once again of the question in the thread, which is essentially: did I create an object that cannot be printed or is it the printer?
And I think here we unfortunately have to say that it is primarily due to the hardware of the printer.
Before you tinker around your Design, you should first improve the print run so that the problem caused by it is largely eliminated.
Good evening!
I want to correct my earlier post slightly. The warping of my test wall was halved by raising the bed temperature by 10 degrees from a true 80 to a true 90 (settings were 90 and 100). And if I added cylinders to each end to both anchor the ends better and provide some resistance to the contraction forces during cooling, the result halved again.
Of course, my second point means that I changed my design to get an improvement. As the previous post says, I have done nothing to correct the source of the problem. I believe that he is also correct that this is fundamental to the printer and the filament. Bambu ASA and Sunlu ABS both produced a similar amount of warping.
As you can see in the picture, the underside is anything but straight and looked no different on the X1C.
I have experimented further and achieved a minimal deviation with my X1C or the print plate, at least over the entire surface. I can’t measure the deviation, I don’t have the means to do so. I therefore estimate the deviation to be <0.08mm or even less. In other words: absolutely acceptable.
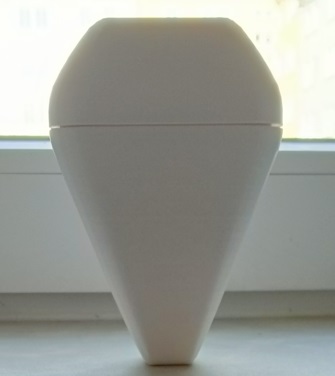
The advantage of a rigid print bed, such as glass, is that the print results are reproducible and practically independent of the design of the print object (Here is my experimental solution: Warped bed :( seems like a common QC issue - #1524 by KanneKaffe). The reproducible result is absolutely acceptable or even better.
Conclusion: If the lower surfaces have to be placed on top of each other, either a small gap, as I show in the picture, or a thin seal between the parts will help. The last housing that I printed with a CR-20 printer was also fitted with a seal for these reasons. But the small gap, as can be seen in the picture, is now sufficient to make the minimal difference in the flatness of the surfaces visually disappear.
Best regards
After two months I receive the Heater and Temperature Controller for the Active Heating System on my X1C! See the link above!
For a possible solution, please see the above link… it took two months to receive the parts I order!